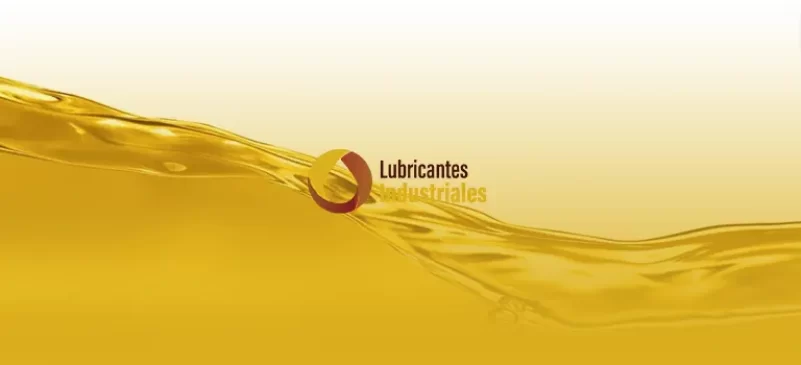
Que es Aceite Térmico
El aceite diatérmico es básicamente un líquido que se utiliza para transportar calor de un lugar a otro, que ha sido previamente calentado por cualquier método capacitado para ello, ya sea un quemador, una resistencia o cualquier otro método.
También se conocen como fluidos de transferencia de calor o del inglés como fluidos de transferencia de calor HTF.
Su origen se encuentra en la destilación del petróleo, a partir de radicales minerales refinados que sufren pequeñas modificaciones que modifican su viscosidad y temperatura de congelación, o cambios químicos, su procesamiento posterior lleva a que este aceite se denomine aceite diatérmico sintético.
En cualquier caso, el aceite diatérmico, que representó una verdadera revolución tecnológica frente a otros sistemas convencionales, es útil en procesos que requieren altas temperaturas (de 180 a 280 ° C), pero operando a baja presión, así como en procesos que Requieren calefacción y refrigeración en la misma unidad.
Entre las características del Aceite Térmico se encuentran
- Elevada estabilidad térmica con alta resistencia a la oxidación convirtiéndolo en un fluido muy eficiente.
- Por su naturaleza química, presenta una mayor resistencia a la oxidación.
- Elevado calor específico, permitiendo un contenido de calor máximo por unidad de volumen.
- Alta conductividad térmica para una rápida transferencia de calor.
- Baja viscosidad, facilitando una mejor transmisión de calor.
- Excelente fluidez a baja temperatura mejorando los arranques en frío.
- Baja presión de vapor, disminuyendo las pérdidas por evaporación y evitando la tendencia que tienen los fluidos térmicos convencionales a formar bolsas de gas que generan cavitaciones provocando pérdidas de carga a las unidades de bombeo.
- Optimo poder lubricante que favorece la buena conservación de las bombas y válvulas.
- Los problemas de corrosión son inexistentes.
- Su bajo riesgo posibilita la ubicación de las calderas en las propias naves de trabajo sin necesidades de obra civil especial.
- Al trabajar siempre en fase líquida, sin cambios de estado durante el proceso, conlleva un ahorro energético importante en comparación con el tradicional y convencional circuito de vapor pérdidas entálpicas de los condensados.
- Los aceites térmicos tienen una vida útil aprox. 3 a 5 años. Normalmente, los que soportan una mayor temperatura son también los que tienen una mayor vida útil en condiciones normales.
- Se van degradando con el tiempo y uso. Cuando se degradan, pierden sus características originales, se carbonizan y se incrustan dentro de los tubos, poniendo en peligro la vida útil del calentador de aceite.
- Es recomendable llevar a cabo un estricto control sobre la calidad de los mismos, sacando muestras del aceite en circulación constante (no del tanque de expansión) y mandándolas analizar semestralmente con el proveedor del mismo, para que nos indique el grado de pureza del mismo.
- Con este control semestral del aceite térmico, se podrá uno percatar de la necesidad del cambio necesario de aceite térmico.
- Cuando llega el momento de cambio, será necesario una limpieza total del sistema, eliminando cualquier rasgo de humedad (sopleteo con un gas inerte).
- Recordemos que los aceites térmicos no son compatibles entre sí, por lo que no se deben mezclar.
- Cualquier residual de carbonización o incrustación dentro del sistema debe ser eliminado cuidadosamente por medio de una limpieza química agresiva con recirculación con una bomba de acero inoxidable por parte de personal especializado y altamente calificado en este tipo de limpiezas.
- Un sistema de calentamiento con aceite térmico, para su mejor entendimiento, tiene un comportamiento similar al del cuerpo humano.
- El serpentín multitubular de transferencia de calor es similar a las venas y arterias de nuestro cuerpo. La bomba recirculadora de aceite térmico es el corazón. El aceite térmico vendría siendo nuestra sangre. El quemador del calentador junto con su ventilador equivale al sistema digestivo y respiratorio del cuerpo.
Usos y aplicaciones del Aceite Térmico
- Recomendable para procesos que requieran de altas temperaturas y procesos industriales de alta productividad.
- Secado: pinturas, tintas, cerámicas, tabacos, textiles y papel.
- Ramas textiles.
- Fabricación en serie de madera prensada.
- Freideras industriales: papas fritas.
- Reactores químicos.
- Tanques de petróleo.
- Hule, plástico y fibra.
- Generación de vapor sin quemador.
Elección del aceite diatérmico
La elección correcta debe hacerse en función de la temperatura máxima de la película y no de la temperatura media.
Un calentador de tubos múltiples distribuye sus cargas uniformemente sobre varios tubos paralelos.
Su temperatura máxima de película es menor que la de un radiador con uno o dos tubos paralelos.
A medida que se acerca la temperatura máxima recomendada por el fabricante, el fluido del radiador se degrada a la temperatura máxima de la película, acortando la vida, carbonizando y obstruyendo los tubos de calor.
Por lo tanto, un calentador de aceite diatérmico requiere una verificación semestral del estado del aceite diatérmico.
Cualquier aumento de presión por encima indica el inicio de la degradación del aceite diatérmico y, por lo tanto, una posible carbonatación o deposición similar al aceite.
La prevención de fugas comienza con la instalación. Unas conexiones, uniones y cierres de seguridad que encajen debidamente pueden reducir considerablemente el riesgo de fugas.
Un uso consciente del material aislante puede también ayudar a evitar que las pequeñas fugas se enciendan o dejen quemaduras y manchas.
También son importantes los materiales utilizados para el calentador de inmersión, la carcasa y el tanque. Los materiales deben ser capaces de soportar las temperaturas y las propiedades químicas del fluido térmico para prevenir un fallo.
El mantenimiento, el material aislante y los materiales correctos son parte de la solución, la solución más simple es cambiarse a un calentador eléctrico por fluido térmico.
Los sistemas eléctricos de fluido térmico no utilizan una llama abierta, lo cual reduce el riesgo de encendido. Además, pueden ofrecer calentamiento directo, lo cual los hace mucho más eficientes.
También es importante utilizar sensores adecuados. Por ejemplo, si la velocidad de flujo se hace muy lenta, ello puede elevar la temperatura del tubo, creando así un riesgo de fracturación.
Es importante tener en cuenta el material aislante alrededor de áreas vulnerables como las válvulas y los cierres de seguridad. Esto significa prevenir las fugas escogiendo un material aislante no poroso.